Variation is simply deviation from expectation. The size, trends, nature, causes, effects, and control of this variation is the centre of Six Sigma methodology.
By attending the one-day Introduction to Lean Process Improvement Training Course delivered by pdtraining in Sydney, Melbourne, Perth and other cities, you will learn the ways to improve processes using lean methodologies.
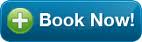
If you toss a coin ten times, you could expect five heads and five tails. But the reality of variation and the concept of odds actually shows us that there is a 50/50 chance on each throw, despite what the previous toss result was or what the next toss result will be.
Theoretically you could toss a coin 100 times and get 100 heads. So when you toss the coin ten times, and do it over and over again, the output varies for each set of tosses. The extent to which the results deviate from expectation is the extent to which variation has occurred.
If you continuously measure something that occurs many times it’s going to vary around an average or “mean-value”.
Describing variability over a period of time helps us understand how the system is working and to predict how it will continue to vary in the future.
Common Cause
When variation is produced by the system itself it is known as “common cause” variation. You can attempt to reduce common cause variation but you cannot eliminate it due to the nature of the system in place.
- These include human systems, for instance how long it takes to process a loan application.
- The amount of a time a tyre mechanic takes to change the tyres on a car
- A sales clerk processing a credit card payment
Special Cause
This type of variation is directly caused by something “special” or out of the ordinary. Again this type of variation is impossible to predict, let alone remove from a process.
- If the post is delivered to your mailbox at 2:00 pm each day but today it was raining and the post arrived at 3:30pm, that’s a “special cause” of variation.
- If the network system goes down that manages your email, that’s a special cause.
Tampering
A common mistake is trying to improve a specific process by adjustment when it does not need adjusting.
The term for this mistake is called tampering. Tampering usually occurs when the measured internal outcome does not meet our external performance targets. Examples of external performance targets can be financial targets, and demands to meet monthly quotas.
- Tampering is the adjustment of a stable process.
- If the process is not statistically stable, its performance is unpredictable.
- Tampering leads us to respond to a false alarm, since a false alarm is when we think that the process has shifted when in actuality it hasn’t.
Structural
These changes are a result of regular, systematic changes in output. They will be more pronounced over the long term and through seasonal patterns. These changes are normal and reflect an ebb and flow of normal production being influenced by the environment.
- The organisation invests in a new piece of machinery which doubles output but does not take into account product storage capacity.
- A fleet of new delivery vans is enlisted, but the manufacturing capacity was not adjusted to fulfill the new delivery capacity.
Each type of variance has its own type of analysis and solution and this is where we find the Lean process improvement is more of an art form which requires customised analysis and integration compared to Six Sigma which is the science of improvement.
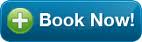
Comments are closed.