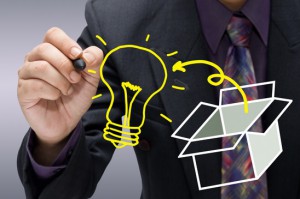
Pdtraining delivers 1-day Lean Process Improvement Training Course delivered by pdtraining in Canberra, Adelaide and other cities.
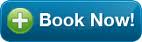
In previous articles we’ve considered the Kano method and the TPS process, and in this article we focus on what is known in the manufacturing world as Muda.
Muda is the waste and work that does not add any value to the product and that the customer would not pay for if given a choice. All waste has a cost that is direct loss to the manufacturing company.
In Lean and Six Sigma manufacturing, the focus is aimed at identifying and eliminating three common types of waste:
- Muda (Waste)
- Muri (Strain/Overburden)
- Mura (Unevenness)
Now let’s learn how we can eliminate these three types of waste from the manufacturing process.
Muda
Muda is the waste or work that does not add any value to the product. There are seven kinds of Muda in the Toyota Production System:
- Unnecessary Motions
- Waiting for work and materials
- Transportations
- Overproduction
- Processing
- Inventories
- Corrective Operation (rework and scrap)
Mura
Mura is the variation in the operation of a process not caused by the end customer. It is the Irregular, Inconsistent, Uneven, and Unbalanced work on machines.
A typical example of Mura is when employees are rushing production all morning only to stand around and do nothing later in the day.
Muri
Muri means putting excessive demand on equipment, facilities, and people caused by Mura and Muda. Muri is pushing a machine or person beyond natural limits. Overburdening people results in safety and quality problems. Overburdening equipment causes breakdowns and defects
Examples of Muri include pushing too hard, lifting heavy weight or repeating a tiring action again and again.
The New Wastes
In addition to the three basic types of waste, lean principles have identified other sources of waste in businesses:
- Waste of untapped human potential.
- Waste of inappropriate systems
- Wasted energy and water
- Wasted materials
- Waste of customer time
- Waste of defecting customers
- Waste of unused creativity
Once an organisation has gone through the process of identifying the wastes in their particular manufacturing division(s), improvement is just a few steps away.
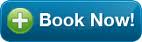
Pdtraining delivers 1000’s of professional development courses each year in Brisbane, Sydney, Parramatta, Melbourne, Adelaide, Canberra and Perth, so you can be assured your training will be delivered by a qualified and experienced trainer.
All public Lean Process Improvement Training courses include am/pm tea, lunch, printed courseware and a certificate of completion. Customised courses are available upon request so please contact pdtraining on 1300 121 400 to learn more.

Comments are closed.